Voicepicking: de sleutel tot krachtige orderverwerking
Efficiënt orderpicken is essentieel voor de werking van uw magazijn. Het heeft een direct invloed op zowel uw productiviteit als de klanttevredenheid. Maar zelfs in de best ontworpen magazijnen zijn uitdagingen zoals incidentele fouten, veiligheidsrisico’s en de druk om op tijd te zijn, gebruikelijk. Een fout van een orderpicker kan potentieel enorme gevolgen hebben voor uw klanten. Door Voicepicking te integreren, kan uw magazijn aanzienlijke verbeteringen zien op deze gebieden. Op deze manier wordt een sneller, veiliger en nauwkeuriger orderpickproces gecreëerd.
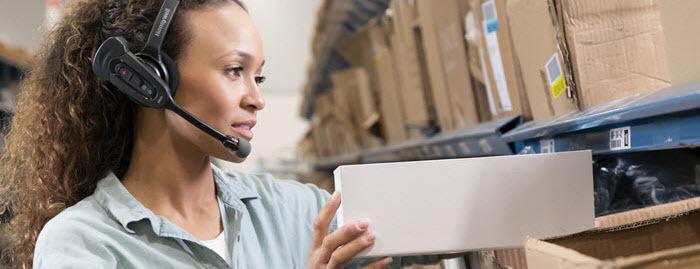
De problemen met traditioneel orderpicken
Traditioneel orderpicken is een taak met hoge vraag en hoge snelheid. Het vereist een unieke balans tussen snelheid en nauwkeurigheid. Fouten kunnen optreden wanneer pickers lijsten verkeerd lezen, de verkeerde items pakken of items helemaal vergeten. Dit kan gemakkelijk leiden tot ontevredenheid bij de klant. Bovendien, met ogen die op schermen of papieren lijsten zijn gericht, lopen ze vaak een hoger risico op ongevallen, zowel voor zichzelf als voor waardevolle goederen. Daarom heeft u een oplossing nodig die zowel fouten als risico’s vermindert.
Hoe voicepicking orderverwerking transformeert
Voicepicking (of spraakgestuurd picken) is een gestroomlijnd alternatief waarmee pickers handsfree kunnen werken. Alles wat uw pickers nodig hebben, is een paar headsets en een microfoon. Uitgerust met een headset en microfoon ontvangen pickers realtime verbale instructies die hen naar het exacte item en de locatie binnen het magazijn leiden. Deze oplossing stelt werknemers in staat om acties verbaal te bevestigen, waardoor hun handen en ogen vrij blijven om zich te concentreren op veilig en nauwkeurig picken.
De sterke punten van spraakgestuurd picken
Snellere inwerktijd
Door het geven van gesproken orders werkt het systeem volledig intuïtief. Daarom heeft u geen complexe trainingsmethoden meer nodig om uw medewerkers op te leiden. Dit verkort de trainingstijd drastisch. Nieuwe medewerkers, inclusief tijdelijk personeel, kunnen zeer snel beginnen met het picken van orders.
Hogere productiviteit
Met spraakopdrachten kunnen werknemers zich uitsluitend richten op het daadwerkelijke orderpicken, wat de productiviteit en efficiëntie verhoogt.
Verminderde foutmarge
Spraakgestuurd picken vermindert fouten dankzij realtime controlecijfers en verbale bevestiging, wat zorgt voor nauwkeurigheid van begin tot eind.
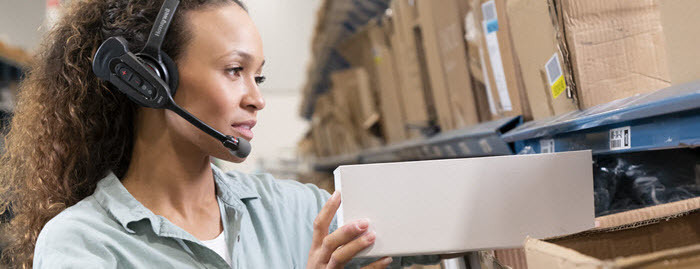
Spraakgestuurd picken in actie
Gekoppeld aan het Warehouse Management-systeem van 3PL Dynamics biedt spraakgestuurd picken naadloze communicatie. Terwijl uw medewerkers de verbale aanwijzingen volgen, monitort ons WMS elke pick in realtime, corrigeert onmiddellijk fouten en volgt de voorraadniveaus om de voorraad te optimaliseren en items indien nodig aan te vullen. Deze integratie zorgt ervoor dat elke pick nauwkeurig is, waardoor foutmarges worden verminderd en de snelheid waarmee u orders verwerkt, wordt verbeterd.
Een toekomstbestendige oplossing
Voicepicking technologie tilt de gebruikersinteractie naar een hoger niveau. Daarom wordt verwacht dat het gebruik ervan in het magazijn alleen maar zal toenemen. Naarmate meer magazijnen AI-gedreven, handsfree oplossingen adopteren, kunnen papieren lijsten en handscanners beter tot het verleden behoren.
Magazijnbeheer: Alle ins en outs onder controle
Uw magazijn is de hoeksteen van uw logistieke operatie. Waar u aan de logistieke behoeften van uw klanten voldoet. Natuurlijk wilt u dat zo goed mogelijk doen. Daarom is een state-of-the-art WMS cruciaal voor uw huidige en toekomstige succes. Een state-of-the-art Warehouse Management-software voor 3PL-logistiek helpt u te winnen.